Automatisch von KI übersetzt, Original lesen
Welche konkreten Innovationen prägen die Zukunft?
12 März 2024
Der am häufigsten verwendete vom Menschen erzeugte Stoff auf der Erde hat sich über Jahrtausende entwickelt, doch das nächste Jahrzehnt voller Innovationen wird für die Branche von entscheidender Bedeutung sein, wenn sie ihre ehrgeizigen Nachhaltigkeitsziele erreichen will, berichtet Mitchell Keller.
„Wenn die Leute mich fragen, was ich mache, dann antworte ich immer: ‚Haben Sie die Feuersteins gesehen?‘“, sagt Joel Galassini, Executive VP der kommerziellen Zementabteilung von Cemex, einem Baustoffunternehmen mit Sitz in Mexiko.
„Familie Feuerstein“ ist ein US-amerikanischer Zeichentrickfilm aus den 1960er Jahren, der in einer romantisierten Steinzeit spielt.
Seine scherzhafte Antwort lässt darauf schließen, dass die Branche, in der er arbeitet, altmodisch ist.
„Ich beschreibe mich selbst als einen Cartoon aus der Steinzeit, aber wir haben so viele Leute, die die Jetsons sind“, fügt er hinzu.
Die Jetsons waren die Hauptfiguren einer anderen amerikanischen Zeichentrickkomödie (die einfach „Die Jetsons“ hieß) aus den 60er Jahren, die einer Familie in einer idealisierten Zukunftskulisse folgte.
Ein sich entwickelnder Sektor
Während Galassini diese Anekdote erzählt, liegt direkt über seiner Schulter der Südbereich des Las Vegas Convention Center; bis zum Rand vollgestopft mit hochentwickelter Bauausrüstung, Technologie und hochmoderner Wissenschaft, die für die World of Concrete 2024 ausgestellt werden.
Es habe einige Zeit gedauert, sagte der Vizepräsident von Cemex, aber er glaube, dass die Betonindustrie mit großen Schritten in die Zukunft schreiten werde.
„Wir nutzen KI in vielen unserer Betriebsabläufe, wir setzen Drohnen ein, wir beschäftigen uns mit autonomen Fahrzeugen und all diesen Dingen … Ich beschreibe es als die Familie Feuerstein, aber in Wirklichkeit passiert bei uns eine Menge ‚Jetson-artiges‘ Zeug“, sagte er.
CO2-arme Lösungen
Ob aufgrund unternehmensinterner Vorgaben, staatlicher Vorschriften oder vertraglicher Bestimmungen: Die Betonindustrie musste rasch enorme Fortschritte bei der Herstellung von mehr Produkten aus Recyclingmaterialien mit geringerem CO2-Fußabdruck machen.
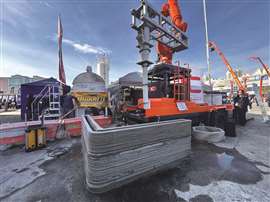
Um die Nachfrage der Verbraucher zu befriedigen und Umweltauflagen einzuhalten, haben viele Unternehmen ihren Zementherstellungsprozess umgestaltet. Zement ist ein wichtiger Bestandteil von Beton, aber auch einer der weltweit größten Kohlenstoffproduzenten.
Dies führte zu einem verstärkten Engagement seitens der Wissenschaftsgemeinschaft, die weltweit nach kohlenstoffärmeren Lösungen für Zementmischungen suchte, darunter auch Forscher der Empa, der Eidgenössischen Materialprüfungs- und Forschungsanstalt.
„Die wichtigsten Innovationen bei Zement und Betonprodukten der letzten Jahre wurden von der Notwendigkeit getrieben, die Nachhaltigkeit zu verbessern und die Emissionen zu reduzieren“, bestätigt Dr. Mateusz Wyrzykowski, Gruppenleiter für Betontechnologie am Beton- und Asphaltlabor der Empa.
Graphen, Hanf, Kaffee und eine Vielzahl neuer spezieller synthetischer Stoffe und Zusatzstoffe finden ihren Weg in Beton und Zement. Die Ergebnisse und Absichten sind unterschiedlich, aber das Experimentieren ist von größter Bedeutung, um bahnbrechende Produkte zu entdecken, die zur Emissionsreduzierung beitragen können.
„Durch die Abfallreduzierung und den verantwortungsvollen Umgang mit Ressourcen wurden erhebliche Fortschritte erzielt“, ergänzt Wyrzykowski.
Eines der spannendsten Materialien für Zement, das die Empa untersucht hat, ist „Biokohle“. Dabei handelt es sich um ein kohlenstoffreiches Material, das durch Pyrolyse von Biomasse entsteht. Anders gesagt handelt es sich um das Bioprodukt, das bei der Erhitzung organischer Materialien ohne Sauerstoff entsteht.
Theoretisch könnte Beton aus organischen Materialien, der mit Biokohlezement hergestellt wird, Kohlenstoff aus der Atmosphäre entfernen. Derzeit wird Biokohle erfolgreich als Dämmstoff eingesetzt.
Einige Produkte sind bereits auf dem Markt, die Empa geht jedoch davon aus, dass durch weitere Forschung eine stärkere, sicherere Version eines Biokohle-Zusatzes entwickelt werden kann.
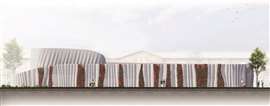
„Biokohle ist sehr porös. Sie nimmt viel Wasser auf, aber auch teure Zusatzstoffe, die bei der Betonherstellung verwendet werden“, erklärt Wyrzykowski. „Sie ist schwierig zu handhaben und auch nicht ganz ungefährlich.“
Der feine Biokohlestaub sei problematisch für die Atemwege des Menschen und berge Explosionsgefahr, heißt es in der Empa.
Daher wird weiterhin untersucht, ob das Material zu Pellets verarbeitet werden kann.
„Solche Leichtzuschlagstoffe gibt es bereits aus anderen Materialien wie Blähton oder Flugasche“, sagt Wyrzykowski und verweist auf einige Vorläufer. „Das Know-how im Umgang mit diesen Materialien ist in der Industrie vorhanden, und das erhöht die Chancen, dass das Konzept in die Praxis umgesetzt wird.“
Neuanalyse der Zementproduktion
Zurück bei Cemex sagte Galassini, sein Unternehmen habe Produkte mit weniger Klinker als herkömmlicher Zement und Produkte mit Flugasche hergestellt, was beides zur Reduzierung der Kohlendioxidemissionen beitrage.
Genauso wichtig sei jedoch eine Neuanalyse der gesamten Zementproduktion, um die chemische Zusammensetzung anzupassen, sagte er.
„Anstelle von Kohle verbrennen wir in unseren Öfen andere Dinge“, sagt er. „Wir können recycelte Abfallprodukte verbrennen. Wir können Reifen verbrennen, wir können Abfallbrennstoffe verbrennen, wir können Industrie- und Haushaltsabfälle verbrennen … Wir können Vieh und Kuhkadaver aufnehmen und alles auf verantwortungsvolle Weise entsorgen und damit die Öfen befeuern.“
Das System, so weist er darauf hin, sei zwar nicht völlig emissionsfrei, die Emissionen seien jedoch stark reduziert und führten zu größeren Vorteilen, darunter Kosteneinsparungen bei den recycelten Brennstoffquellen.
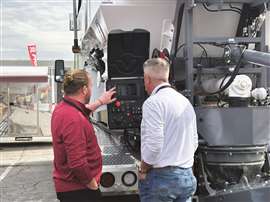
„Unser Zementwerk in Berlin verwendet 98 % recycelte Produkte“, sagt Gassalini und weist darauf hin, dass das Land Mitte der 2000er Jahre von der Deponierung abgekommen ist. „Wir nehmen den gesamten Abfall, pelletieren ihn und verbrennen ihn im Ofen. Anstatt ihn also auf einer Deponie zu entsorgen und Methan zu erzeugen, das meiner Meinung nach 30-mal wirksamer ist als CO2, können wir diesen Abfall verbrennen, Zement herstellen und ein Produkt daraus machen.“
Diese Denkweise ist kein Einzelfall. Die meisten großen globalen Akteure verfolgen aggressive Ansätze zur Reduzierung des CO2-Ausstoßes und zur Förderung der Kreislaufwirtschaft.
Die deutsche Heidelberg Materials Group hat 2023 eine Reihe kohlenstoffärmerer Produkte auf den Markt gebracht und plant, bis Ende 2024 in einem Zementwerk in Norwegen eine Anlage zur CO2-Abscheidung und -Speicherung (CSS) zu eröffnen.
„Unser CSS-Projekt im norwegischen Werk Brevik begann Mitte der 2000er Jahre als ehrgeizige Idee“, sagte ein Sprecher von Heidelberg.
„Aus den ersten Überlegungen entwickelte sich eine Desktop-Studie. Im Dezember 2020 erteilte die norwegische Regierung ihre endgültige Genehmigung und Unterstützung für den Bau der weltweit ersten Anlage zur Kohlenstoffabscheidung im industriellen Maßstab in einem Zementwerk.“
Im Rahmen dieses Projekts soll Kohlenstoff vom Standort in einen Unterwasserspeicher transportiert werden.
„Sobald die Anlage in Betrieb ist, sollen jährlich 400.000 Tonnen CO₂ abgeschieden und per Schiff zu einem Terminal an der norwegischen Westküste transportiert werden“, erklärte Heidelberg. „Von dort wird das verflüssigte CO₂ per Pipeline zu einem Speicher unter der Nordsee transportiert, wo es dauerhaft gespeichert wird.“
Obwohl die Methoden zur Abscheidung und Speicherung von Kohlenstoff noch nicht perfekt sind, wies Heidelberg darauf hin, dass dies lediglich ein Hebel für nachhaltige Innovation sei.
„Wir dekarbonisieren unser Produktportfolio weiter durch konventionelle Maßnahmen zur Kohlenstoffreduzierung“, erklärte das Unternehmen. „Unsere Teams arbeiten seit Jahren daran, den Klinkeranteil in unseren Produkten zu reduzieren, das Produktportfolio umzustellen und den Anteil alternativer Brennstoffe zu erhöhen.“
Maschinen unterstützen Innovationen
Während Beton und Zement physikalische Veränderungen durchlaufen, müssen auch die Maschinen, die die Substanz mischen und gießen, mit der Zeit Schritt halten.
Volumetrische oder mobile Mischfahrzeuge sind nichts Neues, aber Fortschritte in der Computertechnologie, der Materialspeicherung und der Datenkatalogisierung haben diese bereits wertvollen Werkzeuge in der modernen Zeit noch wertvoller gemacht.
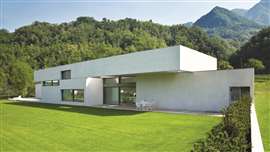
Cemen Tech bezeichnet sich selbst als den weltweit größten Hersteller von Lösungen zur volumetrischen Dosierung und kontinuierlichen Betonmischung und ist seit der Gründung im Geschäft der volumetrischen Mischung tätig.
Da alle benötigten Betonmaterialien auf dem LKW und auf der Baustelle gelagert und gemischt werden, werben die Projektmanager mit Einsparungen beim Transport. Die hochentwickelte Technologie der Einheit stellt jedoch auch sicher, dass der Abfall begrenzt wird und die Betonproduktion den Erwartungen hinsichtlich der Aufgabe und des Klimas entspricht.
Zach McQuay, der McQuay Construction in Oklahoma, USA, leitet, verwendet eine C-Serie von Cemen Tech und ist begeistert von der Ordnung, die eine Maschine bei einem Auftrag schaffen kann.
„Sie haben die volle Kontrolle“, sagt er. „Es ist eine mobile Betonmischanlage, wir müssen also nicht fahren. Wir können das gesamte Material vor Ort laden und legen mit nur drei LKWs täglich 402 m zurück.“
Im Vergleich zum Einsatz einer Transportbetonanlage außerhalb des Standorts schätzte McQuay, dass für einen ähnlichen Auftrag 20 oder mehr Lkw erforderlich wären, zuzüglich der Fahrtzeit sowie des Be- und Entladens.
Mit einem volumetrischen Mischer, sagt McQuay, „machen wir erst dann Beton, wenn wir auf ‚Start‘ drücken. Wir bekommen frischen Beton auf Abruf.“
Lufttests können vor Ort durchgeführt werden und der Mischer kann jeweils kleine Chargen herstellen, was laut McQuay den Abfall reduziert.
„Wenn in der Welt der Fertigmischungen der Lufttest nicht besteht, wird die gesamte Ladung abgelehnt“, erklärte er und merkte an, dass volumetrische Mischer einfach eine neue Charge herstellen können (und zwischendurch Anpassungen an der Mischung vornehmen). „Wenn wir in der volumetrischen Welt den Lufttest vermasseln, haben wir weniger als eine halbe Schubkarre zum Recyceln.“
Da zur Herstellung von Beton auf dem LKW Sand, Steine, Wasser, Chemikalien und Kunststoffe benötigt werden, können Benutzer über eine Computerschnittstelle die genaue Zusammensetzung ihrer Mischung verwalten und bei Bedarf anpassen.
„Wir haben ein Echtzeit-Wasser-Zement-Verhältnis. Wir haben eine Echtzeit-Dosierungsrate unserer Chemikalien. Wir haben eine Echtzeit-Bewertung unseres Sandes, Gesteins und Wassers, sodass wir in der Lage sind, jeden dieser Aspekte während des Projekts jederzeit anzupassen“, fügte McQuay hinzu.
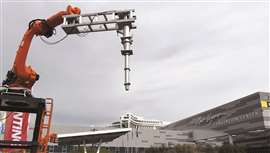
Durch die Protokollierung der Daten entsteht ein Netzwerk zuverlässiger Informationen, auf die Fertiger oder Verleger bei ähnlichen Arbeiten oder in vergleichbaren Umgebungen zurückgreifen können.
Auch Fortschritte in den Bereichen künstliche Intelligenz, 3D-Scannen und -Drucken sowie Sensortechnologie haben Straßenfertigern und anderen Betonmaschinen große Vorteile gebracht. Ein Gleitschalungsfertiger der deutschen Wirtgen Group ist ein Beispiel dafür.
„Beim Betoneinbau mit Wirtgen-Gleitschalungsfertigern können verschiedene Automatikfunktionen wie das AutoPilot 2.0-System oder der automatische Dübeleinsetzer genutzt werden“, so das Unternehmen. „Das von Wirtgen entwickelte 3D-Steuerungssystem AutoPilot dient zur präzisen, leitdrahtlosen Steuerung von Gleitschalungsfertigern bei der Erstellung von Versatz- und Einzugsprofilen aller Art.“
„Die Erstellung eines geodätischen Datenmodells durch einen Vermesser ist nicht mehr notwendig. Der Auf- und Abbau eines Leitdrahts, wie er bei einer herkömmlichen Maschinensteuerung üblich ist, entfällt.“
„Die Maschine bewegt sich mit Satellitenortung entlang eines virtuellen Leitdrahts. Sowohl die Höheneinstellung als auch die Lenkung der Maschine werden automatisch gesteuert.“
3D-Druck und Beton
Einer der verlockendsten und visuell anregendsten Fortschritte in der Automatisierung im Betonbereich ist der 3D-Druck.
Zu den beliebtesten Vorführungen auf der World of Concrete gehörten 3D-Drucker mit schichtweiser Extrusion, die mithilfe einer gesteuerten Düse eine Zementpaste präzise Schicht für Schicht herauspressen.
Die „zahnpastaähnlichen“ Betonhaufen können so hoch gebaut werden, wie es der Drucker oder die Umgebung zulassen. Einige Drucker sind groß genug, um ganze Gebäude zu drucken.
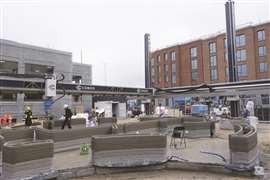
Ein 3D-Drucker von COBOD International, einem in Dänemark hergestellten Produkt, hat letztes Jahr in Heidelberg das angeblich größte 3D-gedruckte Gebäude Europas fertiggestellt. Das Gebäude ist 54 m lang, 11 m breit und 9 m hoch.
Der 3D-Drucker COBOD BOD2 kann neben Kastenstrukturen auch nicht quadratische geometrische Formen erstellen. Der Bau begann Mitte 2023 und dauerte etwa 172 Stunden.
„Wir gehen davon aus, dass die Drucker bis zu fünf oder zehn Jahre halten“, sagt Philip Lund-Nielsen, Mitbegründer von COBOD, und merkt an, dass die Lebensdauer der Maschinen zunimmt. „Sie bestehen zu 90 % aus verzinktem Stahl. Die meisten Probleme unserer Kunden vor Ort bestehen darin, die richtigen Materialien zu verwenden. Wenn sie das erst einmal beherrschen, werden sie wirklich effizient.“
Alles zusammenfügen
So wie Beton ein Produkt ist, das aus bestimmten, zusammenwirkenden Elementen besteht, müssen die Branchenführer auch weiterhin zusammenarbeiten, um das Produkt voranzubringen.
„Wir arbeiten wirklich mit Eigentümern, Architekten und Ingenieuren zusammen, um sicherzustellen, dass wir ein Gebäude, einen Gehweg oder eine Fahrbahn richtig und nicht überdesignt entwerfen“, sagt Galassini. „Sehen Sie sich den Beton an, der in den meisten Gehwegen einer Stadt verwendet wird. Es ist eine von der Stadt festgelegte Rezeptur.“
„Mit diesem Rezept entsteht ein Gehweg, der, sagen wir, eine Festigkeit von 6.000 bis 8.000 PSI hat, was einer Flughafenlandebahn entspricht. Ich kann also eine 747 auf einem Gehweg landen, der nur eine Festigkeit von 2.500 PSI benötigt.“
Angesichts all dieser Informationen und der verfügbaren Technologien zur Bekämpfung dieses Beispiels von Over-Engineering ist Galassini der Ansicht, dass es an der Zeit ist, langfristige Lösungen zu finden.
Und diejenigen, die nicht modernisieren und zur Lösung des Problems beitragen, könnten auf der Strecke bleiben.
„Ich bin überzeugt“, sagt Galassini, „dass die Leute, die weiterhin innovativ sind und die Dinge vorantreiben, höchstwahrscheinlich die Gewinner sein werden. Diejenigen, die sich gegen Veränderungen sträuben, werden irgendwann an einem Wendepunkt stehen, an dem sie plötzlich keine andere Wahl mehr haben oder vielleicht zu spät dran sind.“
|
Bleiben Sie verbunden

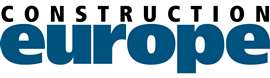
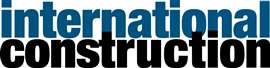
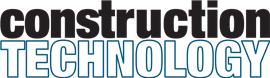
Erhalten Sie die Informationen, die Sie brauchen, genau dann, wenn Sie sie benötigen – durch unsere weltweit führenden Magazine, Newsletter und täglichen Briefings.
Mit dem Team verbinden
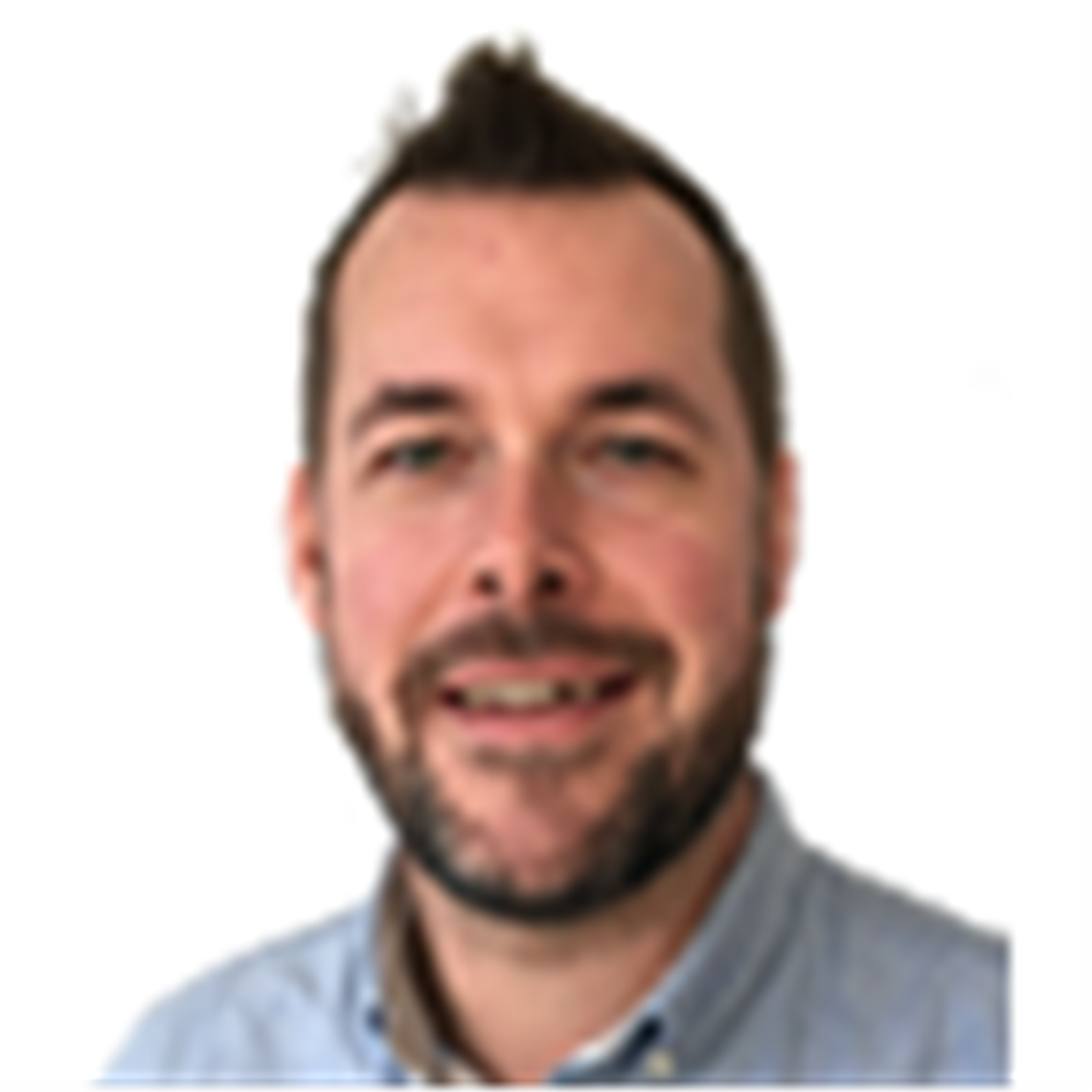
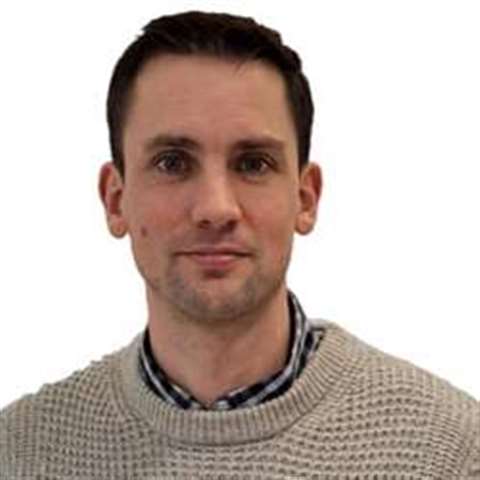
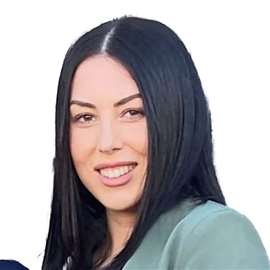
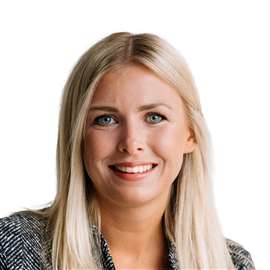