Automatisch von KI übersetzt, Original lesen
Wie Strabag ungewollt einen Tunnel-Weltrekord brach
12 Februar 2024
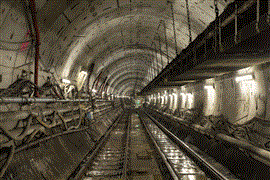
Tief unter der Erde und ohne dass es die Menschen merken, die oben die Ruhe des englischen Nationalparks North York Moors genießen, frisst sich eine Tunnelbohrmaschine (TBM) langsam, aber sicher durch harten Fels.
Die Herrenknecht-TBM und das dafür verantwortliche Team – Hauptauftragnehmer Strabag im Auftrag des Auftraggebers, des Bergbauunternehmens Anglo American – haben bereits den Weltrekord für den längsten einzelnen TBM-Vortrieb der Welt gebrochen. Dieses Kunststück gelang ihnen, als der Tunnel mit 4,9 m Durchmesser Ende letzten Jahres eine Länge von 25,8 km erreichte.
Bei nun über 27 km haben sie noch weitere 10 km vor sich, womit sie den Rekord sicher vor allen anderen Herausforderern brechen werden.
Was das Ganze in mancher Hinsicht noch beeindruckender macht, ist die Tatsache, dass niemand wusste, dass das Projektteam einen Rekord brechen würde, als es mit dem Tunnelbau begann.
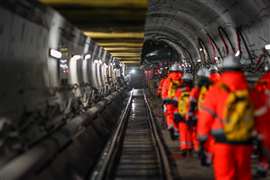
Anglo American erhielt die Genehmigung, die weltweit größte bekannte Lagerstätte von Polyhalit, das als Düngemittel verwendet wird, unter streng geschütztem Moorland abzubauen, solange die Mine in der Nähe von Whitby an ihre Verarbeitungs- und Vertriebsanlage in Teesside unterirdisch angeschlossen war. Frühe Konzepte für das Projekt sahen vor, das in Salzlake gelöste Polyhalit durch eine flache unterirdische Pipeline zu transportieren.
Doch das Bergbauunternehmen entschied sich letztlich für die nach eigenen Angaben umweltfreundlichere Variante eines Tunnels, der bis zu 360 m tief unter dem Nationalpark verläuft. Ursprünglich war geplant, drei Tunnelbohrmaschinen einzusetzen, von denen eine an jedem Ende des Tunnels und eine in einem Zwischenschacht startet.
Die erste Tunnelbohrmaschine, die von den Grundschulkindern der Gegend Stella-Rose getauft wurde, wurde 2019 von der Oberfläche in Teesside aus gestartet. Die beiden anderen sollten später aus 380 m unter der Erde liegenden Schächten gestartet werden.
Doch die Fortschritte mit der ersten TBM waren so gut, dass Anglo American noch im selben Jahr mit Strabag eine Vereinbarung traf, die Tunnelvortriebe auf zwei zu reduzieren. Der längere der beiden wäre an sich schon ein Rekordbrecher gewesen, aber das Team war sich dessen zunächst noch nicht bewusst. Und noch später entschied man sich, bei nur einer TBM zu bleiben, was einen noch größeren Rekord bedeutete.
Gute Bodenverhältnisse und ein starkes Team
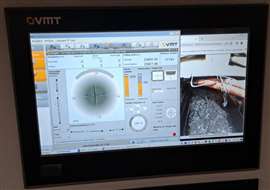
Craig Sewell, Projektleiter bei Strabag, begründet die Entscheidung wie folgt: „Die Leistung der TBM übertraf all unsere Erwartungen. Dazu trugen eine Reihe von Faktoren bei. Dazu gehörten die guten Bodenverhältnisse, die Qualität der Ausrüstung des TBM-Herstellers und die Tatsache, dass wir über ein großes Team erfahrener Leute verfügen, die diese Ausrüstung bedienen und die Arbeit erfolgreich durchführen.“
Trotz der Größe des Projekts sei es laut Sewell dank der Bodenverhältnisse nicht so komplex wie andere große Tunnelprojekte.
„Anfangs herrschen von der Startrampe aus wechselnde Bedingungen, da wir durch Tone und Geschiebemergel vordringen müssen, aber ziemlich schnell gelangen wir in den Redcar-Schlammstein, ein trockenes, stabiles Gestein, und der restliche Vortrieb unseres TBM bleibt innerhalb dieses Gesteinsbands“, sagt Sewell.
„So erhalten Sie eine ziemlich konstante Vortriebsgeschwindigkeit und können den Verschleiß der Scheiben und anderer Teile der Ausrüstung ziemlich gut vorhersagen. Wir durchlaufen zwar Verwerfungen, aber bevor wir mit dem Projekt begannen, hatten wir viele gute Daten über die Verwerfungszonen und das, was wir durchliefen, wurde an diesen Daten ausgerichtet.“
Im Frühjahr dieses Jahres kommt es zu einem längeren technischen Stopp des Projekts, bei dem einige Schneidkopfsanierungen vorgenommen werden und ein Belüftungsschacht auf der Lady Cross Plantation im Nationalpark an den Tunnel angeschlossen wird.
Danach, so Sewell, werde das Team für das gesamte Jahr 2025 und bis ins Jahr 2026, in dem die Tunnelarbeiten voraussichtlich abgeschlossen sein werden, zum Dauerbergbau zurückkehren.
Neue Herausforderungen
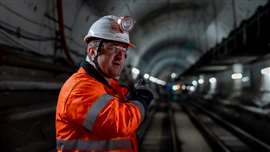
Die Änderung der Anzahl der am Woodsmith-Tunnel beteiligten Tunnelbohrmaschinen verlief allerdings nicht ohne Herausforderungen, wie Mark Pooleman, Gebietsleiter von Anglo American für den Tunnel, betont.
„Als wir diese erste TBM in Betrieb nahmen, war alles für einen 12,5 km langen Tunnelvortrieb ausgelegt. Vom Förderband, das das Mineral exportiert, über die Kommunikation bis hin zu den Rettungsverfahren – als wir diese grundlegenden Entscheidungen trafen, die Lieferstrategie von drei TBMs auf zwei TBMs und jetzt auf eine TBM zu ändern, handelte es sich um ein Änderungsmanagementverfahren, bei dem es nicht nur um Kleinigkeiten ging“, sagt er.
„Es ist ein Teamansatz und ein Verdienst aller Ingenieure auf beiden Seiten, die herausgefunden haben, wie diese Dinge funktionieren und wie wir ein 27 Kilometer langes Förderband haben können, das jede Woche länger wird.“
Sewell fügt hinzu: „Die Tunnellänge bringt einzigartige Herausforderungen mit sich. Derzeit haben wir 27 km Infrastruktur – die Mörtelleitungen, das Förderband, die Schienen. Es steckt also eine Menge Arbeit in der Wartung und in der Planung der Wartungszeiten im Vergleich zur Betriebszeit der TBM. Das gesamte Team kann viel darüber lernen, wie wir unsere Effizienz bei all diesen Herausforderungen maximieren können.
„Wir pumpen derzeit 15 km lang Mörtel von Lockwood Beck [einem Reservoir zwischen Guisborough und Whitby] zur TBM, was meiner Meinung nach völlig beispiellos ist. All diese Herausforderungen erfordern eine enorme Teamleistung von Anglo American über uns selbst bis hin zu den wichtigsten Lieferanten, um sicherzustellen, dass wir diese kritischen Probleme im Griff behalten.“
Aufgrund der logistischen Herausforderungen, die ein einzelner Tunnelvortrieb mit sich bringt, und der zusätzlichen Arbeitskräfte, die zur Lösung dieser Probleme erforderlich sind, gibt es laut Pooleman „Vor- und Nachteile“ bei der Verwendung einer TBM anstelle von drei, und es hat sich in Bezug auf die Kosten „keine großen Veränderungen“ ergeben. Anglo American soll bisher 2 Milliarden Pfund (2,5 Milliarden US-Dollar) für die Entwicklung des Woodsmith-Projekts ausgegeben haben, während die gesamten Entwicklungskosten bis zu 7 Milliarden Pfund (9 Milliarden US-Dollar) betragen könnten.
Den Rekord brechen
Es gab jedoch noch andere Belohnungen, nicht zuletzt ein Erfolgserlebnis, als dem Team klar wurde, dass es einen Weltrekord gebrochen hatte.
„Ich bin unglaublich stolz, Teil des gesamten Projekts zu sein. Ich denke, es ist ein unglaublicher Gewinn für die Region und für ganz Großbritannien. Und dass wir mit diesem Tunnel einen Weltrekord aufgestellt haben, ist großartig“, sagt Pooleman.
Auch Sewell ist zufrieden. „Das ist ein schöner Meilenstein, den wir erreicht haben und der für das Team ein Grund zum Feiern ist. Das Projekt hat noch viel mehr zu bieten, worauf wir stolz sein können, und es bringt der Region noch viel mehr, worauf wir ebenfalls sehr stolz sind.“
Aber er möchte sich auch weiterhin auf die bevorstehende Aufgabe konzentrieren. „Wir können uns nicht darauf ausruhen, Weltrekordhalter zu werden. Wir haben noch 10 km vor uns, also konzentrieren wir uns darauf. Das ist immer noch die Länge eines normalen Tunnelbauprojekts. Die wahre Feierlichkeit kommt bei 36,7 km“, fügt er hinzu.
An diesem Punkt würde auch das Guinnessbuch der Rekorde diese Leistung bestätigen – im Moment hat das allerdings wenig Sinn, da das Projektteam mit den immer weiter vordringenden Tunnelbohrmaschinen jeden Tag weiter Rekorde bricht.
Pooleman legt auch Wert darauf, Mapeis Rolle bei der Bereitstellung des Injektionssystems hervorzuheben, und lobt den TBM-Hersteller Herrenknecht. „Sie haben die Maschine geliefert und uns unglaublich unterstützt, wenn man bedenkt, dass wir nicht zwei weitere Maschinen von ihnen gekauft haben“, sagt er.
Andreas Leppert, Senior Project Manager Traffic Tunnelling bei Herrenknecht, ergänzt: „Dieser Weltrekord-TBM-Vortrieb ist etwas, auf das wir definitiv stolz sind. Wir gratulieren Strabag und Anglo American zu dieser beeindruckenden Leistung beim Woodsmith-Projekt. Mit Stella-Rose haben die Mineure einen neuen Meilenstein im maschinellen Tunnelbau gesetzt.“
Pooleman fasst zusammen: „Wir sehen die Nutzung eines solchen Tunnels zum Export unseres Minerals als echte Innovation für die Bergbauindustrie. Das bedeutet, dass wir das Produkt nie auf einen Zug oder Lastwagen verladen müssen, sodass der CO2-Fußabdruck beim Abbau und Export dieses Produkts reduziert wird. Die Mine selbst ist im Vergleich zu dem, was sie sonst wäre, winzig, sodass sie nur sehr geringe Auswirkungen hat. Dieser Tunnel ist ein hochmoderner Bestandteil des Projekts, das wir als bahnbrechende Neuerung für die Bergbauindustrie insgesamt betrachten.“
Bleiben Sie verbunden

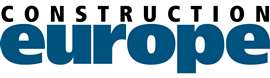
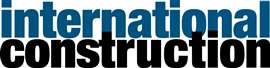
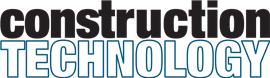
Erhalten Sie die Informationen, die Sie brauchen, genau dann, wenn Sie sie benötigen – durch unsere weltweit führenden Magazine, Newsletter und täglichen Briefings.
Mit dem Team verbinden
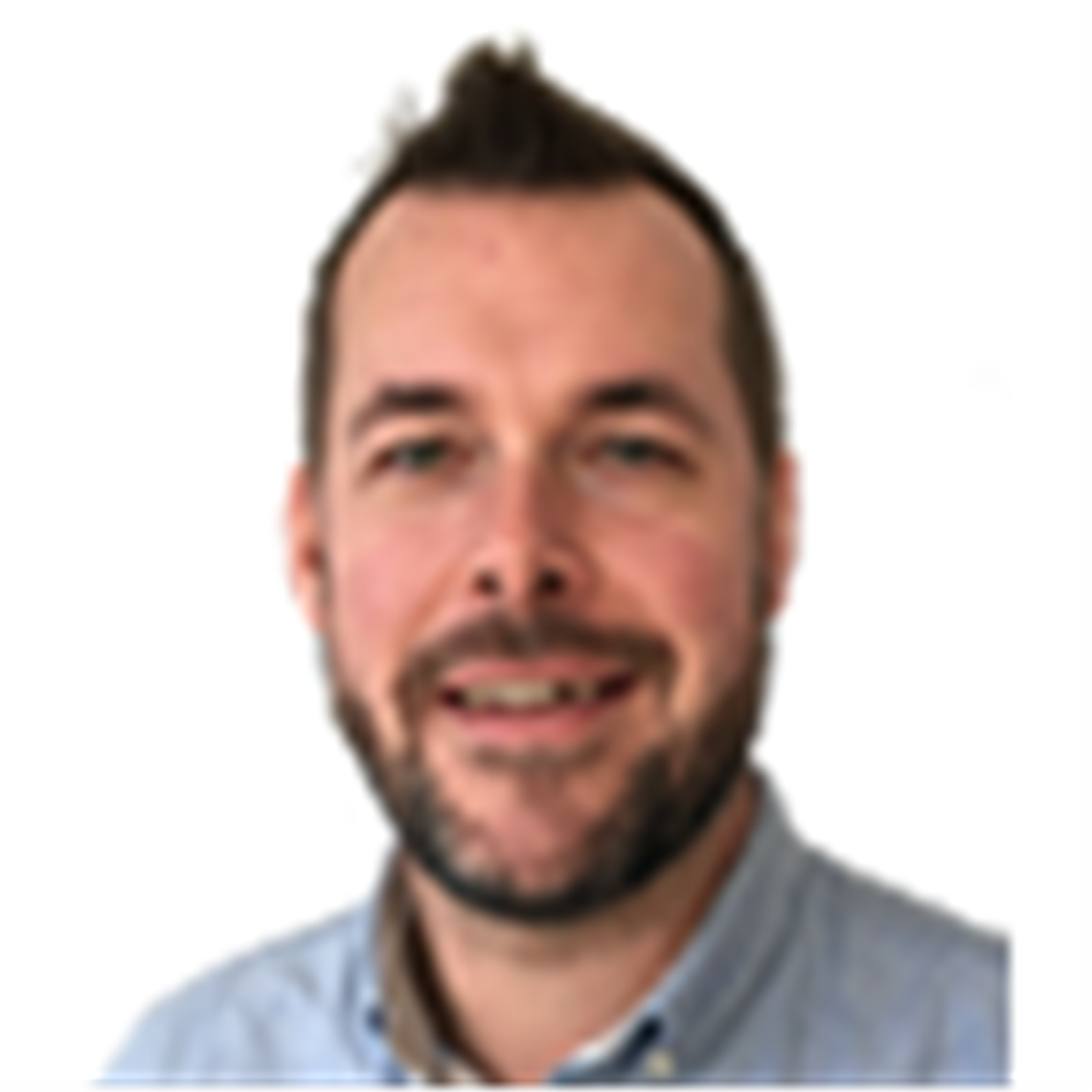
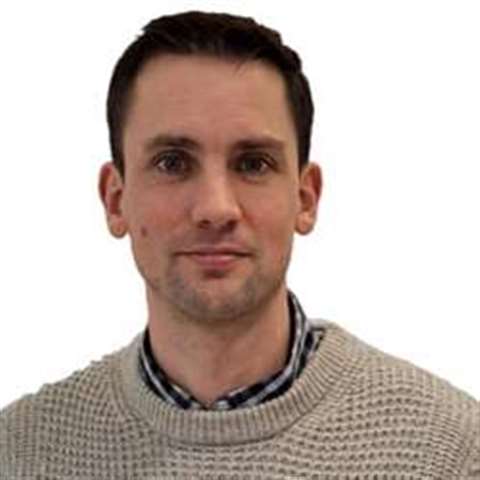
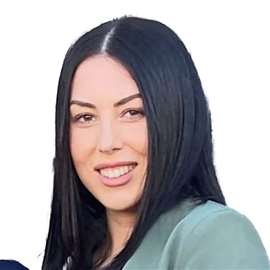
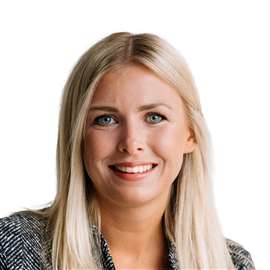